Articles
Follow our developments and deepen your industry knowledge by following our updates and news.
Searching for new, better, and innovative solutions. Digital Transformation at Polpharma API.
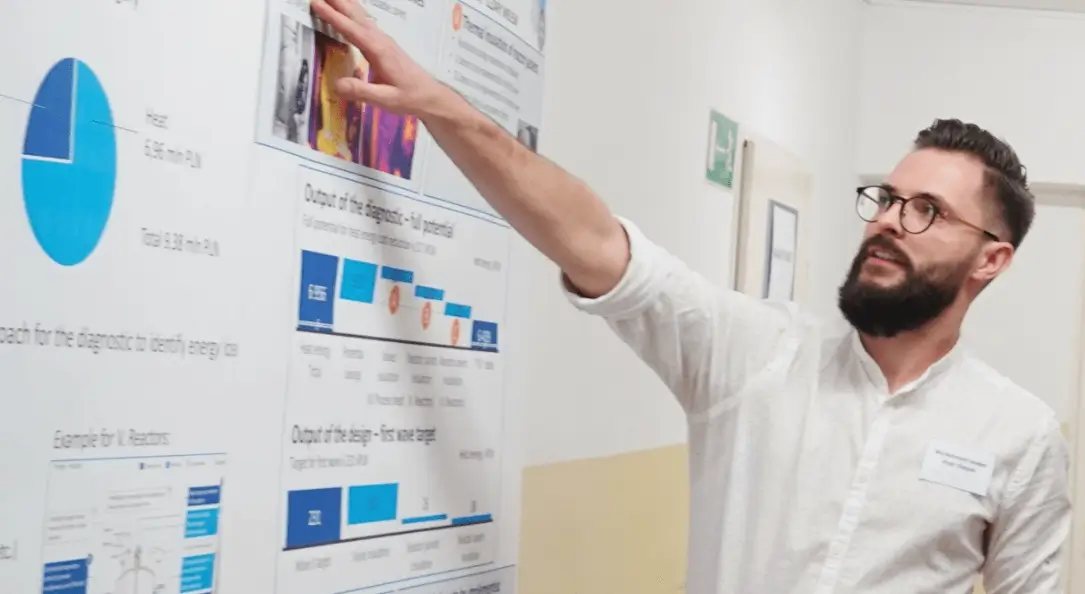
People and their ability to change are the key drivers of each transformation. Observations show that it is the human element in transformational processes that requires the greatest attention. It is necessary to consciously change and adjust both the organizational culture - attitudes and behavior - and hard competencies. Implementing new technology does not transform an organization if this change is not understood and supported by its members.
Magdalena Kuć-Kawczyńska/ Marketing Manager API
MKK: How would you describe the transformation of Polpharma API Business Unit (API BU)?
Mateusz Godzisz: Transformation of API BU is a long-term program that covers not only the single unit operations to achieve a specific goal or benefit, but it’s more about the holistic approach. It’s about maintaining and growing operations consistently and sustainably, according to the latest trends that dominate the manufacturing sector.
What do you mean by latest trends?
Damian Bogacki: We relate here to Industry 4.0. Currently, manufactures have plenty of opportunities to utilize advanced tools and technologies throughout the product lifecycle. It helps increase operational visibility, reduce costs, shorten production times, and deliver exceptional customer experience.
What are the key elements of transformation in API BU?
MG: One of the inherent elements of the development of any organization is the search for new, better, and more innovative solutions. The API BU is undergoing a transformation process, and Digitization is its inseparable element. The other key component of transformation is the Capability Building.
How does this refer to Polpharma API’s strategic direction?
MG: Key element of Transformation is creating Production System which drives the change. This is collection of best practices applied in the organization, which are based on management philosophy. It consists of the foundation: People, Compliance, and Values, then the pillars: Equipment Care, Improvement, Supply Chain, Performance Management, and a Vision that sets the direction for the organization to build increased agility, responsiveness, and resilience. So, all this is directly aligned with the recently approved strategy of Polpharma API.
What can you say about the Production System initiative?
MG: The main goal of this system is to build skills to eliminate eight types of wastes at each level of the organization and involve each of us in problem-solving, quality improvement, safety, and cost reduction processes. The most important thing is that our people create all content, such as procedures, tool descriptions, and other elements for our people. Therefore, everything is the result of combining our knowledge and the characteristics of our organization.
Works with the Production system initiative are ongoing since 2020 and will continue until the end of 2021. Many of the components are already implemented.
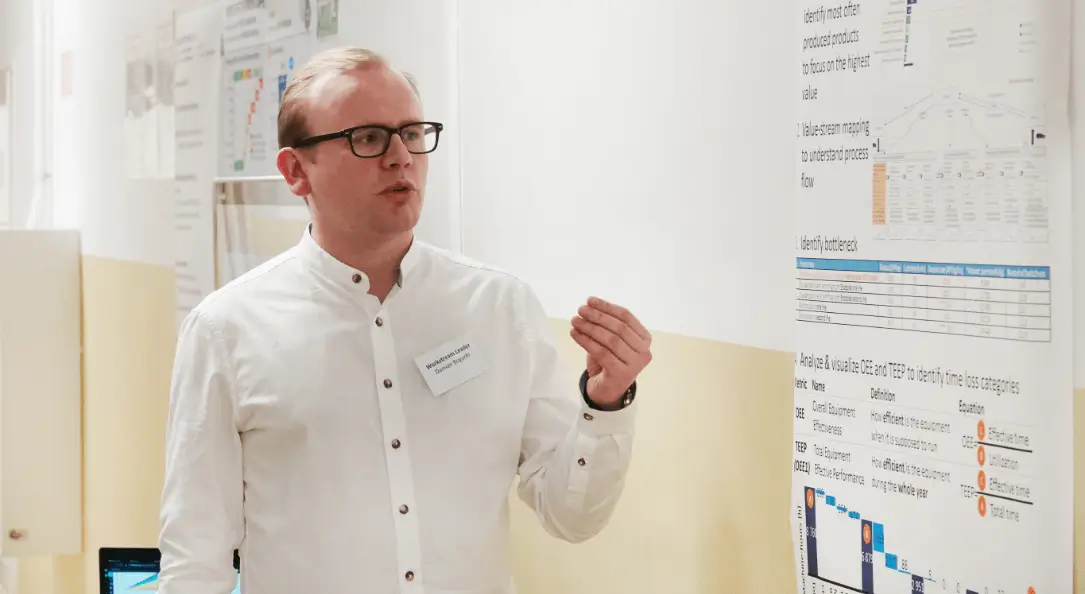
What are the digital initiatives that are currently ongoing at API BU?
DB: Over the past two years, we have introduced and continue to improve the Electronic Shift Handover (ESH). Thanks to the ideas of people working with this tool daily, we’ve already introduced several changes and improvements. One of the most significant upgrades so far was the development and introduction of the Maintenance module, which allows monitoring and reporting the process performance. Data collected in this way enables monitoring necessary indicators regarding failure repair times in various dimensions, which in turn may contribute to an increase in the efficiency of using the equipment in our plant.
It shows a high level of complexity. How do you deal with this challenge?
DB: That’s right, the complexity level is very high, and ESH is not the only digital initiative. In Q4 2020, another pilot digitization project began. It is a pioneering initiative at Polpharma group level. Digital Replica is a project aimed at improving production efficiency by building digital representations of selected production processes. For this purpose, we collect data from various sources like ORACLE, data from sensors installed directly on the devices/reactors, Electronic Shift Handover, paper batch reports and many others. This tool allows not only to collect a massive amount of data but also to find the relationship between them. Knowledge aggregated in this way enables process engineers to identify process improvement opportunities.
Somebody said that digital transformation begins with people first and then technology…
DB: Yes, all these innovative solutions bring advanced analytical methods and elements of machine learning to everyday work. But of course, this requires the hard work and commitment of many people from API Production, IT, Industrial Automation, and Process Engineers. This is more than sure that the coming months will bring many new ideas and initiatives based on our findings along the way.
What benefits do you see behind the transformation of the API Business Unit?
MG: First of all, we are talking about leveraging our employees’ innovation mindset and skills. This is also about leveraging new methodologies and technologies, leading to improvements in efficiency and productivity. With the implementation of new elements in our daily work and building skills of using tools and knowledge about operational excellence, we broadly implement the concept of “Lean”. Without these elements, you will not be able to continue and maintain the effects of the work that we can already see, whether in the production areas or the processes efficiencies or energy. It’s a positive change that boosts the engagement of our employees and their motivation to strive for excellence.
Authors
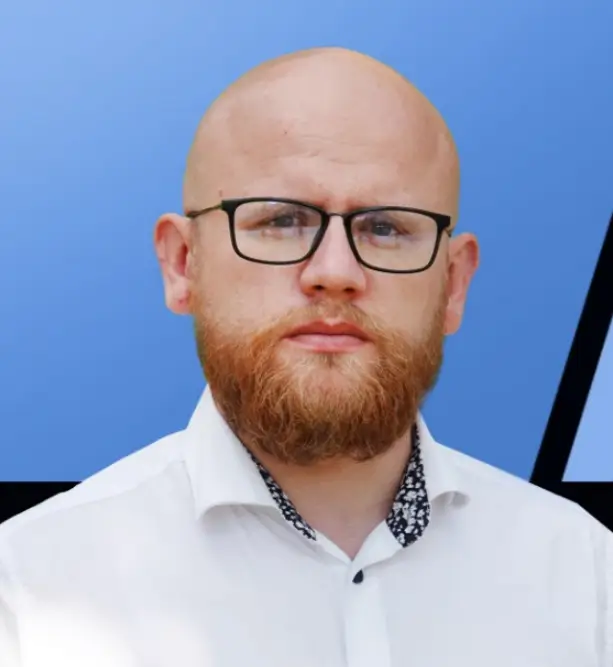
Maintenance Coordinator
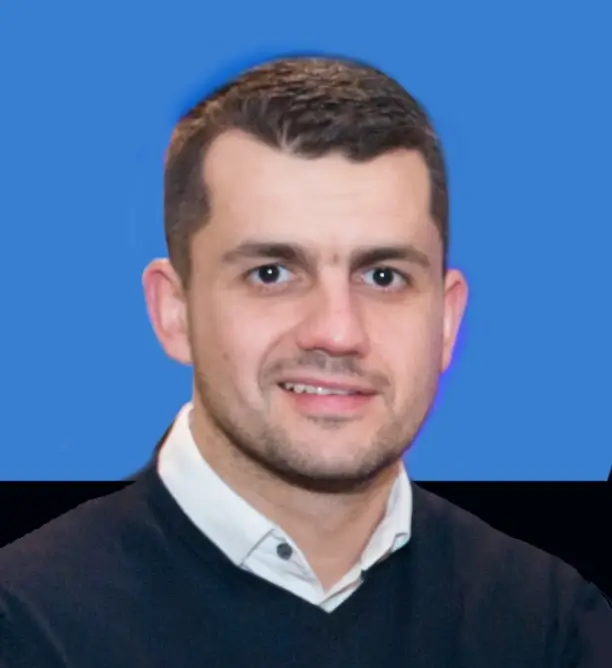
Senior Manager of the Project Management and Operational